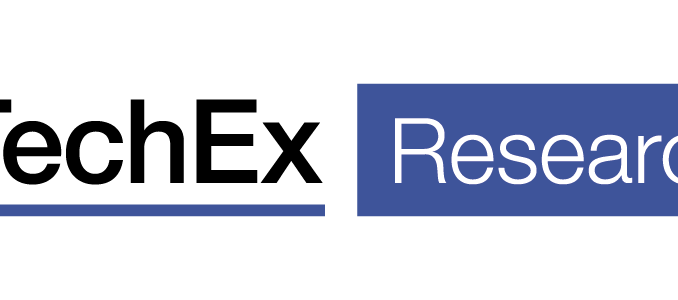

Author: Dr Jack Howley, Technology Analyst at IDTechEx
In March, the printed electronics industry flocked to Munich once again for the LOPEC 2024 conference and exhibition. Featured were some of the latest printed electronics technologies addressing global mega-trends such as vehicle electrification, healthcare personalization, industry 4.0, and sustainability.
With over 170 companies present and over 250 conference talks, there was a lot to digest. Here are three things IDTechEx learned at this year’s conference.
Source: IDTechEx analyst at LOPEC 2024.
Electrification is opening the door to greater printed electronic integration in vehicles
Electrification demands a rethinking of almost every component within a vehicle. There is a market pull for technologies that reduce weight and power consumption to extend battery range while offering complementary premium features to the passenger.
Printed electronics technology providers were, as usual, out in force to demonstrate their suitability to meet these challenges. This included printed armrest heaters integrated with LED lighting and in-mold electronics for component connectivity across entire interior surfaces. BMW and Eink even showed off their concept cars with color-changing exteriors.
Yet despite the ongoing demand for optimized power efficiency and low weight, printed technology solutions have historically struggled to obtain high volumes of orders into the automotive market. This is usually attributed to higher associated costs or regulatory barriers compared with incumbent solutions. Despite some industry disillusionment, a killer application with the potential to tip the scales toward printed technology is emerging: battery management.
LOPEC highlighted the surge in interest for thermal management and hot-spot detection technologies. Popular solutions featured printed and flexible sensor technology capable of spatial temperature and pressure mapping alongside active heating. Large area printed sensor arrays that measure pertinent physical metrics (e.g. swelling and heating) offer localized and granularized feedback to enhance cell deployment during charging and discharging.
The use of multifunctional large area printed sensors enables the integration of thermal management solutions with minimal impact on weight and size while also aiming to satisfy the needs of anticipated regulatory and safety requirements. While the exact timeline of new regulations remains uncertain, in the interim, technology providers are well positioned to remain agile in meeting bespoke customer needs, from the research and development of new battery materials to active battery monitoring during operation.
IDTechEx offers a more detailed analysis of printed and flexible sensors in their latest report on the topic, “Printed and Flexible Sensors 2024-2034: Technologies, Players, Markets”. This report critically evaluates eight printed sensor technologies and provides 10-year market forecasts for revenue and volume demand.
Downstream value chain cultivation will boost chances of printed electronic success
Cultivating downstream collaboration was a frequent talking point this year at LOPEC, the need for which was evidenced by the top-heavy representation of the value chain at the conference and exhibition.
A healthy printed electronics ecosystem has been built over the last few decades through strong partnerships between material suppliers and technology providers. However, for growth potential in key markets to be realized, closer collaboration needs to be replicated with product designers, manufacturers, service providers, and end users. State of the printed electronics value chain and areas for improvement. Source: IDTechEx The automotive sector is already highly vertically integrated, with defined supply chains and close feedback between OEMs, tier suppliers, and end users. This affords a clear route of entry for printed electronics technology and is a key reason the industry is such a major target.
Healthcare is one of the largest potential markets for printed electronics, yet in contrast to the automotive sector, printed technology adoption has been rather sluggish. This is largely attributed to the disparate and disconnected value chain. Moreover, designing a successful business model that incorporates the diverse needs of medical device manufacturers, healthcare providers, insurers, and patients alike is a real roadblock.
For now, a popular strategy for the commercialization of printed electronics in healthcare is providing simple, retrofittable, low-cost sensing solutions. Examples included printed pressure sensors for hospital beds to improve rehabilitation, and leak sensors for ostomy bags to reduce the chance of infection. By integrating low-cost sensors into existing equipment, these solutions slot into existing value chains without needing to reinvent the wheel.
Retrofitting use cases are only a small fraction of the potential applications for printed electronics in healthcare. For the full growth potential to truly be realized, a champion must emerge to focus technology providers on developing value-adding solutions.
One champion looks increasingly likely to be healthcare institutes within the clinical trials space. IDTechEx believes there is an opportunity for the co-development of printed electronics in wearables healthcare to add more data and decentralize clinical trials. Healthcare institutes are poised to couple already sophisticated patient insights and established relationships with doctors with enabling printed electronics technologies for continuous remote monitoring.
Small steps are being made towards sustainability and reducing e-waste
Striking the balance between product performance and sustainable credentials is increasingly difficult. Challenges include the complex material mixture and composition of device stacks. Printed electronics composed of plastic substrates, glues and adhesives, mixtures of metallic and functional inks, pick and place integrated circuits and sensors are hard to disassemble, separate, and recycle. A key link is missing at the point of recovery and separation, and this is preventing functioning circular processes from emerging.
Instead, the focus resides on developing biodegradable and compostable materials. Examples included conductive inks functionalized with biodegradable k-carrageenan moieties, as well as nanocellulose film substrates that can be composted in thirty days. The development of biodegradable and sustainable printed electronics materials is primarily targeted towards use within biosensors and wearable patches. Unlike automotive and industrial applications, which require robust sensors with long lifetimes, the timeline of biodegradation is better suited for disposable smart medical consumables. Likewise, this technology will also be applicable to smart packaging and will benefit from the more established recycling streams of consumer waste.
Conclusion and market outlook
Leveraging established partnerships to build confidence and nurture interest from manufacturers was the focus of printed electronics technology companies at LOPEC 2024. Electrification is driving keen interest in printed electronics technologies, with battery monitoring pitched as the latest major market disruptor. Automotive market progress also highlighted the need for a strategic rethink within the healthcare sector – particularly regarding downstream collaboration. Amongst all of this, the undercurrents of sustainability challenges are lingering. However, these concerns may also be premature for a technology market still grappling with reaching high production volumes.
The stage is set for printed electronics to capitalize on mega-trends in automotive and healthcare, but cultivating greater collaboration downstream will be critical in defining and achieving success.
For more analysis on printed electronics technology, markets, and forecasts, see IDTechEx’s dedicated reports on Printed and Flexible Sensors, Conductive Inks, and 3D Electronics.
For the full portfolio of printed electronics research from IDTechEx, please visit www.IDTechEx.com/Research/PE. Sample pages are available for all reports. |
||